Exploring Sheet Molding Compound Manufacturers
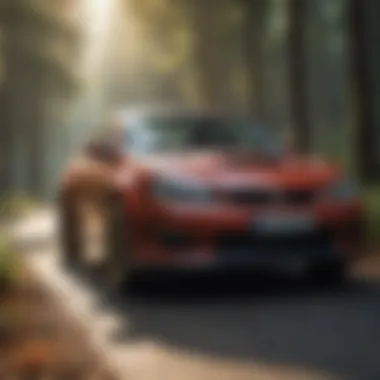

Intro
Sheet molding compounds (SMC) are crucial materials in the modern manufacturing landscape. Their versatility and strength make them ideal for various applications, from automotive parts to consumer goods. The demand for SMC continues to grow, necessitating a closer look at the manufacturers driving this market. Understanding the key players in the SMC sector offers valuable insights into production processes and innovations. This article serves as a guide, exploring essential information about SMC manufacturers, their practices, and their role in sustainability.
Overview of SMC Manufacturing
Importance of SMC in Industry
Sheet molding compounds possess unique properties that set them apart from traditional materials. Their lightweight nature, durability, and resistance to environmental factors contribute significantly to their adoption across various sectors. Industries such as automotive, aerospace, and electrical have increasingly relied on SMC for its high-performance capabilities. Furthermore, as companies push towards sustainable production, SMC has emerged as a favorable alternative to heavier materials like metals and some resins.
Leading Manufacturers in SMC Production
Numerous companies specialize in the manufacturing of sheet molding compounds. Notably, companies like Ashland, Continental Structural Plastics, and AOC Resins play vital roles in this space. These manufacturers invest heavily in research and development to refine their products. They also adhere to strict quality control measures to ensure the reliability and safety of their materials. Such strategies not only bolster consumer trust but align with the industries' push for sustainable practices.
Innovations in SMC Manufacturing
The landscape of SMC production is constantly evolving. Manufacturers are exploring various innovative techniques to enhance material properties and production efficiency. One notable trend is the integration of recycled materials into SMC formulations. This approach not only reduces waste but also lowers production costs. Additionally, advancements in automated manufacturing technology have streamlined production processes, resulting in quicker turnaround times and consistent quality.
"The integration of sustainable practices in SMC manufacturing is not just a trend; it is becoming a necessary component for survival in the competitive market."
Quality Assurance Measures
Ensuring Material Integrity
Quality assurance is a cornerstone of effective SMC manufacturing. Manufacturers implement rigorous testing protocols at each stage of production. These may include tensile strength tests, thermal stability assessments, and environmental resistance checks. Such measures ensure that the final products meet the required industry standards. In turn, this guarantees safety and reliability for end-users.
Industry Standards and Compliance
To align with global standards, SMC manufacturers comply with regulations set forth by various organizations. Compliance with ISO standards, for instance, is essential in affirming a manufacturer's commitment to quality. Furthermore, adherence to these standards facilitates easier market access, enabling manufacturers to expand their customer base across different regions.
Sustainability Practices in SMC Manufacturing
Impact on Environmental Practices
The production of sheet molding compounds inherently has environmental implications. Many manufacturers are actively taking steps to minimize their ecological footprint. This includes optimizing energy usage during production, adopting waste recycling protocols, and utilizing sustainable raw materials. As public awareness of environmental issues increases, the pressure on manufacturers to adopt greener practices also intensifies.
Future Directions in SMC Sustainability
Moving forward, the focus on sustainability in SMC manufacturing will likely deepen. Expect to see increased investment in research aimed at developing biodegradable alternatives to traditional SMC. In addition, collaborative efforts between manufacturers and environmental organizations may yield innovative solutions to enhance both material quality and sustainability.
Ending
The landscape of sheet molding compound manufacturers is intricate and evolving. By understanding the importance of SMC, the leading players in the industry, and the innovations shaping its future, one gains a comprehensive understanding of its role across various sectors. Additionally, a commitment to quality assurance and sustainability reflects the industry's accountability towards both consumers and the environment.
Preface to Sheet Molding Compounds
Sheet molding compounds, often abbreviated as SMC, are a crucial material in various industries such as automotive, aerospace, and electrical appliances. Their significance lies in their unique properties, which combine strength and lightweight characteristics. Understanding SMC is essential for industry professionals to harness its advantages effectively.
Definition and Composition
Sheet molding compounds are thermoset composites, typically made from a mixture of fiberglass, resin, fillers, and additives. They undergo a unique molding process involving a sheet-like form, which allows for a consistent thickness and uniform quality. The resin is usually unsaturated polyester or vinyl ester, which, when combined with fiberglass, creates a strong yet lightweight material. This combination results in high strength-to-weight ratios, making SMC an attractive option for manufacturers looking to optimize their products.
When producing SMC, the composition can be adjusted to meet specific requirements. For example, incorporating different types of fillers can enhance mechanical properties or thermal stability, while additives can improve processing characteristics.
Applications of SMC
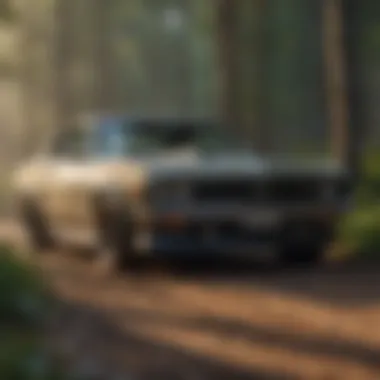

The applications of sheet molding compounds are vast and varied. Here are a few notable examples:
- Automotive Industry: SMC is extensively used in producing vehicle body panels and structural components because it can reduce weight without sacrificing strength. Moreover, SMC components can be molded into complex shapes, enhancing design flexibility.
- Aerospace Sector: Aircraft manufacturers utilize SMC for its high strength and lightweight attributes, which contribute to overall fuel efficiency and performance. Components like aircraft interiors and certain structural elements often use SMC.
- Consumer Goods: SMC finds its place in the production of durable and aesthetically pleasing consumer goods, such as kitchen appliances and outdoor furniture. The materialβs resistance to environmental factors makes it suitable for outdoor applications.
- Electrical and Electronics: Due to their electrical insulating properties, SMC materials are used in applications including electrical housings and components that require thermal resistance and electrical safety.
In summary, sheet molding compounds play a pivotal role across different sectors, providing manufacturers with versatile solutions to meet modern challenges. Understanding the definition, composition, and applications of SMC is crucial for optimizing processes and product outcomes.
Overview of the SMC Manufacturing Process
The manufacturing process of sheet molding compounds (SMC) is a critical aspect of understanding their role in various industries. This stage not only determines the performance and quality of the final product but also addresses the specific needs of different applications. Manufacturing SMC involves carefully selected raw materials and sophisticated molding techniques, making it crucial for manufacturers to optimize these elements to produce high-quality compounds effectively. Moreover, the efficiency of the production process can have a significant impact on costs and environmental sustainability.
Raw Materials Used
The first step in producing SMC is sourcing high-quality raw materials. The primary components typically include:
- Fiberglass Reinforcement: This provides the tensile strength necessary for SMC applications. Various forms of fiberglass, such as chopped strands or continuous roving, can be used based on desired properties.
- Thermosetting Resins: Unsaturated polyester resin is commonly used due to its excellent mechanical properties and resistance to chemicals. Other resins, such as vinyl ester, may also be utilized for specific applications.
- Fillers and Additives: These substances improve performance characteristics. Common choices include talc and calcium carbonate. Additives like UV stabilizers can enhance durability against sunlight exposure.
Ensuring a careful selection of each material is essential. The quality and compatibility of these components directly influence the mixture's performance.
Molding Techniques
Molding techniques employed in SMC production also play a vital role. Here are two widely used methods:
- Compression Molding: This process involves placing the SMC mixture into a heated mold. The mold then compresses the material, allowing it to take shape. After the curing phase, the final product is removed. Compression molding offers good surface finish and part durability.
- Injection Molding: An alternative method, injection molding, entails injecting the mixture into a heated mold under pressure. This technique can produce complex shapes with high precision. However, it requires more initial investment and advanced machinery compared to compression molding.
Both methods have advantages and disadvantages influenced by factors such as product complexity and volume requirements. Evaluating these techniques helps manufacturers select the best options based on their specific production goals.
The efficiency of the manufacturing process impacts both product quality and production costs. Understanding key elements is vital for SMC manufacturers to remain competitive.
Key Players in the SMC Industry
The role of key players in the Sheet Molding Compounds (SMC) industry cannot be understated. They are significant in driving innovation, maintaining quality, and ensuring a stable supply chain within the industry. Their strategies and market behaviors often set the tone for trends and shifts in production techniques, sustainability, and pricing structures. Understanding these players is essential for anyone looking to comprehend the dynamics of the SMC market, whether they are industry professionals, researchers, or stakeholders in eco-friendly material sourcing.
Leading Manufacturers
Several manufacturers stand out in the SMC sector due to their revenue, reach, and technological advancements. Companies such as Lord Corporation, BASF, and SABIC dominate the market, each bringing unique strengths.
- Lord Corporation specializes in advanced composites and has a significant focus on automotive applications, offering innovative formulations that improve performance.
- BASF is a powerhouse in chemicals and has developed a diverse portfolio of SMC products that serve various industries including construction and automotive.
- SABIC stands out for its emphasis on sustainability, producing SMC materials that are environmentally friendly while maintaining high performance.
These leaders focus on continuous improvement and adapt to changing market demands. They invest substantial resources in research and development to enhance the properties and functionality of SMC. Such innovation enables the production of lighter, stronger, and more versatile materials, keeping pace with advancements in related industries.
Market Share Analysis
The competitive landscape of SMC manufacturers showcases a diverse array of players with varying market shares. Recent data indicates that the market is characterized by a few large firms that dominate while a multitude of smaller companies fill niche roles.
- Top Players: The top three players hold approximately 50% of the market share, indicating a significant concentration in production.
- Emerging Companies: Smaller companies, while collectively holding less market share, often excel in specialized applications, thus attracting specific sectors looking for tailored solutions.
Understanding the market share dynamics is crucial as it reflects the influence these companies hold within the industry. Insights into their operating strategies can reveal how innovations in formulations or changes in raw material sourcing impact overall market trends.
In summary, the SMC industry is shaped significantly by its key players. Their approaches to manufacturing and market positioning have lasting implications on trends, product availability, and sustainability initiatives. It is vital for stakeholders to stay informed about these leading manufacturers and the market dynamics that influence the broader SMC ecosystem.
Innovation in SMC Production
Innovation is a vital component of the SMC industry. As pressures for efficiency and environmental sustainability increase, manufacturers are compelled to adapt and enhance their processes. Advancements not only improve product quality but also drive cost-effectiveness. With the right innovations, SMC products can maintain their physical properties while also meeting higher performance expectations.
Advancements in Formulation
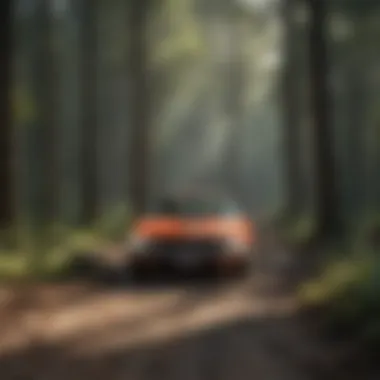

Recent developments in the formulation of sheet molding compounds have led to significant improvements in their durability and functionality. New additives are being integrated to enhance thermal stability, mechanical strength, and resistance to chemicals. For instance, newer types of resins, such as epoxy or vinyl ester, are being favored for their lighter weight and improved performance attributes.
In addition, the use of fillers has evolved. Traditional fillers are now being supplemented with advanced options like nanomaterials. These can provide greater reinforcement at lower volumes, leading to more efficient material use and lighter final products. Manufacturers must ensure that these formulations adhere to industry standards while also meeting performance characteristics.
Emerging Technologies
Emerging technologies are reshaping SMC production by introducing innovations in both manufacturing processes and material science. Automation in the production lines has made manufacturing more consistent and efficient. Technologies such as robotic handling and smart molding machines reduce human error and enhance precision.
Furthermore, advancements in 3D printing technology have started to influence SMC applications. This technology allows for rapid prototyping and can facilitate the creation of complex forms that traditional molding may not accommodate. This can significantly shorten product development timelines and enable customization.
"Emerging technologies in SMC production are crucial for increasing efficiency and adapting to changing market demands."
As SMC continues to be explored in new applications, these innovations will remain essential for maintaining competitive advantage in the industry. A proactive approach in embracing these advancements will be key for manufacturers aiming to thrive in a dynamically evolving marketplace.
Quality Assurance in SMC Manufacturing
Quality assurance in the production of sheet molding compounds (SMC) is crucial. It ensures that materials meet required specifications and performance standards. A reliable quality assurance process enhances the overall integrity of SMC products. It contributes to the safety, durability, and functionality that various industries demand. Without a robust quality framework, manufacturers risk producing subpar materials. Thus, effective quality assurance becomes a paramount concern in the SMC manufacturing landscape.
Standards and Compliance
Standards and compliance play a vital role in quality assurance for SMC manufacturers. Various international and national standards guide production processes. Organizations such as ASTM International and ISO have established guidelines that manufacturers often follow. These standards focus on important aspects like material properties, environmental impact, and production methods. Adherence to these regulations not only ensures product quality but also facilitates market acceptance.
- ASTM D578 outlines the standard specification for SMC materials, addressing character and expected performance.
- ISO 9001 is critical for ensuring that quality management systems are properly implemented.
- REACH Compliance ensures that materials used are safe for both human health and the environment.
Compliance with these regulations helps manufacturers maintain a competitive edge. It builds trust with customers, presenting the company as responsible and dependable.
Testing Methods
Testing methods for quality assurance in SMC production are diverse and sophisticated. Manufacturers utilize a variety of tests to ensure that the final product meets rigorous standards. Common testing methods include:
- Mechanical Testing: This evaluates the strength, stiffness, and durability of the SMC. Tensile strength tests and flexural tests are standard practices.
- Thermal Testing: Testing thermal properties helps determine how the material behaves under heat. Methods such as differential scanning calorimetry (DSC) are used.
- Dimensional Analysis: This is important to ensure that the dimensions of the molded parts meet design specifications. It helps detect deviations that might affect part assembly.
- Chemical Resistance Testing: To evaluate how SMC withstands exposure to various chemicals, tests are performed under controlled conditions.
"Testing is not merely a formality; it is an assurance of value and quality that clients expect."
The data gathered from these tests guide manufacturers in optimizing their processes. It also leads to improvements in product formulations, ensuring that materials perform as needed in their respective applications. Quality assurance through meticulous testing ultimately reinforces the reliability of SMC products in various industries.
Sustainability in SMC Manufacturing
Incorporating sustainability in sheet molding compound (SMC) manufacturing is increasingly essential. The production of SMC has significant environmental implications; thus, addressing sustainability can lead to substantial benefits. This section explores eco-friendly practices and recycling initiatives within SMC manufacturing, considering the environmental and economic advantages for manufacturers and societies.
Eco-friendly Practices
Eco-friendly practices in SMC manufacturing focus on minimizing negative environmental impacts. This involves optimizing resource use and energy efficiency throughout the production process. Here are some notable measures:
- Material Sourcing: Select raw materials that are sustainably sourced. This can involve using renewable resources or choosing suppliers committed to sustainable forestry practices.
- Energy Efficiency: Implement energy-efficient machinery and processes. For example, utilizing energy recovery systems in molding processes can reduce overall energy consumption.
- Chemical Management: Substitute harmful chemicals with less toxic alternatives. This not only protects the environment but also enhances workplace safety.
- Design for Sustainability: Design products with end-of-life considerations. This includes making SMC components easy to disassemble for recycling.
These practices improve the overall carbon footprint of SMC manufacturing and promote a circular economy where materials are reused rather than discarded.
Recycling and Waste Management
Recycling is a critical component of sustainability in SMC production. Efficient waste management strategies can significantly reduce landfill use and improve resource recovery. Here are key aspects to consider:
- Material Recovery: SMC scrap and waste can often be recycled into new products. Manufacturers can establish partnerships with recycling firms to ensure that waste materials are effectively processed and reused.
- Process Optimization: Adjusting the manufacturing process to minimize waste generation can be beneficial. Techniques like closed-loop production systems can reintegrate process waste back into the production cycle.
- Regulatory Compliance: Following local and global recycling regulations is important. This ensures that manufacturers meet legal requirements while also enhancing their sustainability profiles.
Adopting robust recycling practices and comprehensive waste management systems is vital for manufacturers looking to improve their long-term viability and reduce environmental impacts.
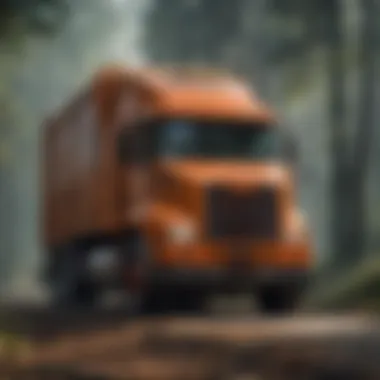

"Sustainability is not a choice, it is a necessity. Manufacturers must adapt to survive in the ever-evolving landscape of environmental responsibility."
In summary, integrating eco-friendly practices and effective recycling strategies in SMC manufacturing can yield considerable advantages for both the environment and the industry. This approach not only aligns with consumer demand for sustainable products but also drives innovation and economic growth.
Challenges Facing SMC Manufacturers
The manufacturing of sheet molding compounds (SMC) presents distinct hurdles that impact overall production efficiency and market viability. Addressing these challenges is critical for manufacturers aiming to maintain a competitive edge in a growing yet fluctuating market.
Understanding these challenges involves a deep dive into the intricacies of raw material sourcing and the complexities of regulatory compliance. Each issue must be managed effectively to ensure sustained production capabilities and product quality.
Raw Material Sourcing Issues
Raw material sourcing is a significant concern for SMC manufacturers. The quality of SMC directly links to the materials used, such as polyester resins, glass fibers, and fillers. Fluctuations in the availability and cost of these raw materials can lead to increased production costs and delays. Furthermore, many of these materials are derived from non-renewable sources, which presents sustainability challenges.
Additionally, manufacturers may face regional supply chain disruptions, whether due to geopolitical tensions, trade restrictions, or logistic hurdles. Building resilient supply chains involves establishing strong relationships with suppliers and exploring alternative materials that can mitigate risks.
Regulatory Challenges
Regulatory compliance poses another layer of complexity for SMC manufacturers. The industry must adhere to stringent guidelines set forth by organizations that govern environmental safety and material usage. Regulations around emissions, waste disposal, and chemical usage are continuously evolving. Staying abreast of such changes requires diligent monitoring and adaptation.
Failure to comply can result in hefty fines and damage to a company's reputation. Moreover, manufacturers must invest in training and auditing processes to ensure adherence to these regulations, resulting in increased operational costs.
Future Trends in SMC Development
As industries evolve, the demand for advanced materials like sheet molding compounds (SMC) continues to grow. Understanding future trends in SMC development is essential for manufacturers and professionals alike. These trends outline opportunities for innovation and highlight challenges that may arise.
Market Growth Projections
The SMC market is anticipated to witness significant growth in the coming years. Reports suggest that the global demand for SMC will rise due to its applicability in a wide range of sectors, including automotive, aerospace, and construction. A few projections indicate that the SMC market might reach a valuation of over $4 billion by 2028. This growth can be attributed to several factors:
- Increased demand for lightweight materials, especially in the automotive industry.
- Greater focus on sustainability and eco-friendly manufacturing processes.
- Advancements in manufacturing techniques, enhancing efficiency and reducing production costs.
- The rise in construction projects that utilize composite materials for their benefits in durability and aesthetics.
Maintaining this growth will require manufacturers to adapt to emerging technologies and market demands while ensuring compliance with environmental regulations.
Research and Development Focus
Research and development play a critical role in shaping the future of SMC. There is ongoing exploration into new formulations and processing methods that can potentially enhance the performance of SMC. Critical areas of focus include:
- Material Innovation: Developing new composite materials that can provide better strength-to-weight ratios and improved thermal resistance.
- Sustainability Research: Investigating bio-based resins and recycling methods to reduce environmental impact. This may involve partnerships with environmental organizations to create more sustainable product lines.
- Thermoplastic SMC: The shift toward thermoplastic SMC is gaining traction. These materials can enable quicker cycle times and better recyclability, meeting growing consumer expectations for sustainability.
"Research and development in SMC must focus on paving the way toward efficient and environmentally responsible production methods."
In summary, future trends in the SMC industry will significantly impact how products are developed and utilized across various sectors. The emphasis on market growth projections alongside a robust research and development strategy will dictate how manufacturers position themselves amidst evolving consumer and industry demands.
Closure
The conclusion of this article focuses on the significant aspects of sheet molding compounds (SMCs) and the manufacturers that contribute to their production. Understanding the role of SMCs is crucial for various industries, ranging from automotive to construction. These compounds are highly valued for their strength, durability, and lightweight nature. They find applications in manufacturing parts that require a combination of flexibility and rigidity.
Summary of Key Insights
The examination of SMC manufacturers reveals several key insights:
- Industry Leaders: Notable companies like Continental Structural Plastics, Molded Fiber Glass Companies, and Royal Composites shape the market with innovative techniques and products.
- Production Process: The manufacturing process involves careful selection of raw materials alongside various molding techniques. These processes are designed to maximize efficiency while ensuring high-quality output.
- Sustainability Initiatives: Increasing eco-consciousness is leading manufacturers to adopt more sustainable practices. This includes developing recyclable SMC products and implementing waste management strategies that minimize environmental impact.
- Technological Integration: The use of advanced technologies in production is not only improving quality but also enhancing the overall performance of SMCs in different applications.
Future Outlook
Looking ahead, the future of SMC development appears promising. Market growth projections suggest an increasing demand for SMCs as more industries recognize their benefits. The ongoing focus on research and development will likely drive innovation, leading to new formulations and applications.
- Innovative Applications: Future trends may see SMCs used in emerging areas such as electric vehicles and renewable energy sectors, where lightweight yet strong materials are essential.
- Regulatory Landscape: Manufacturers will have to navigate evolving regulations, placing emphasis on safety and environmental standards. Compliance will be a critical factor in determining market readiness.
- Collaborative Efforts: The rise of collaborative projects between SMC manufacturers and research institutions may accelerate advancements in materials science, fostering the development of next-generation products.
"The SMC market is poised for transformation, driven by innovation and sustainability efforts across the board."
In summary, the overview of SMC manufacturers highlights their vital contributions to various industries. Their forward-thinking approaches to production, coupled with a commitment to sustainability, will play a crucial role in shaping the future of material use in manufacturing.